Staff Spotlight: Corey Skillman Creates Thoughtful 2025 Honorary Doctorate Awards
Corey Skillman’s journey through the arts is a testament to the kind of hands-on, interdisciplinary education that shapes lasting creative careers. A Cornish College of the Arts Alumni (Fabrication, 2011), Corey has spent the past decade immersed in the college’s creative ecosystem—working in the Jon and Mary Shirley Fabrication Studio (Fab Lab), where students and professionals alike explore the full range of a material-based practice. With nearly 17 years of fabrication experience across industries—from museum exhibit work to boat building—she brings a wide-ranging skill set to every project.
This year, Corey was tapped to design and build the 2025 Honorary Doctorate Awards, drawing on both traditional craftsmanship and emerging technologies. Her story offers a close-up look at what’s possible when fine arts education combines deep technical training, access to industry-level tools, and a strong creative community.
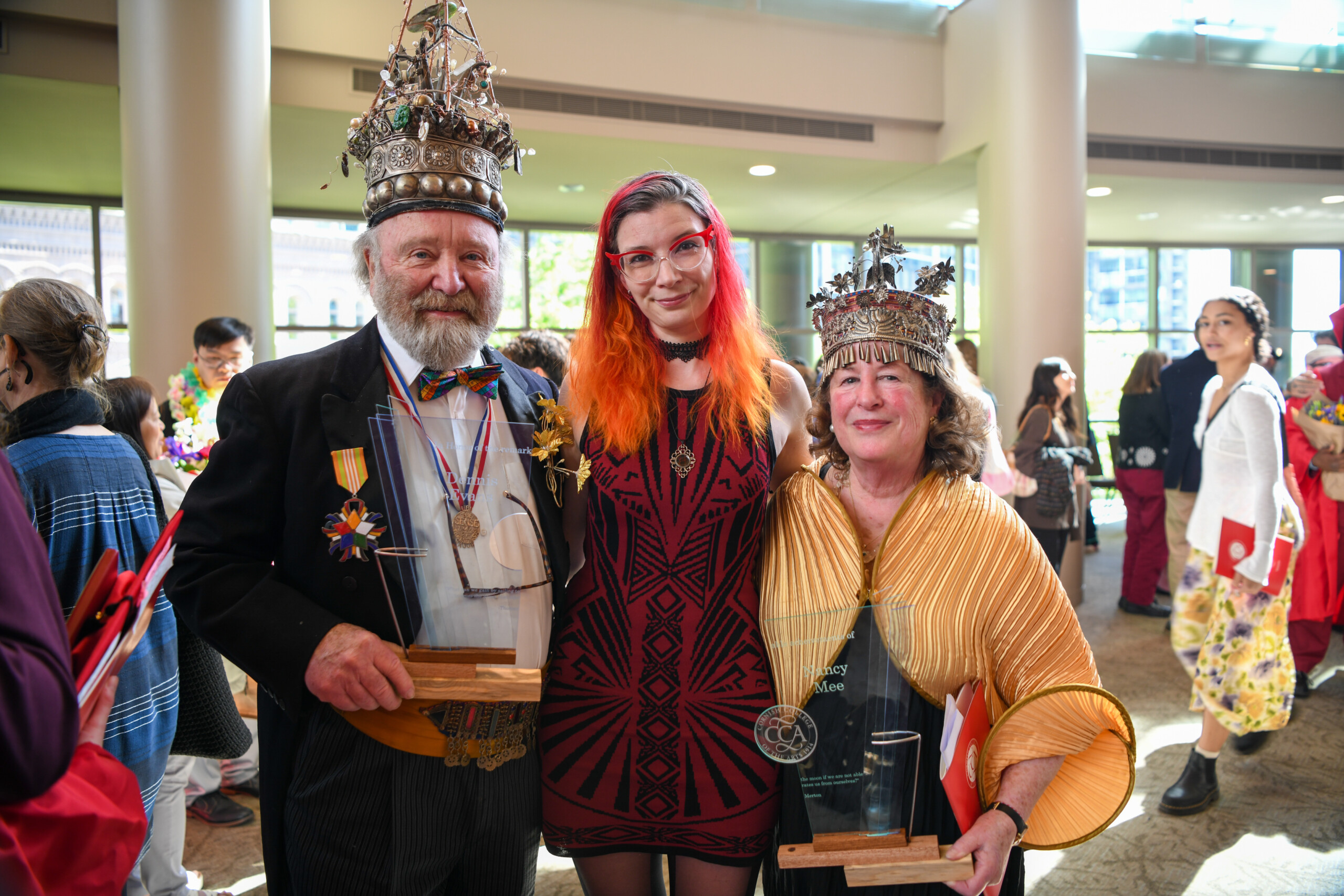
Can you tell us a little bit about yourself?
My name is Corey Skillman (She/her). I came to Cornish for undergrad, kind of fell in love with the place, and worked on and off here as a tech for the past decade. I’ve been working as a high-end fabricator for almost 17 years now.
What is your role at the Fab Lab and how did you get into working with materials and fabrication?
As far as being a fabricator, I grew up on a small farm, so you’re always building stuff in the moment to keep up with things. Doing a lot of that, doing a lot of metal work on the fly, and having fun with it. When I went to school for sculpture, it was a no brainer. After I graduated, I went off to do framework, fine woodworking, and things of that nature. I fell into boat building, realized that fiberglass was way easier than dealing with wooden boats, so I started doing a lot of fiberglassing; I also worked in museums and as a preparator and exhibit fabricator, working closely with curators, conservators, exhibition managers, and things like that. It looked like, “we want a space to look like this, but it has to be built out of these materials to not harm the artifacts,” and just learning about that.
I’ve worked in the Fab Lab on and off for a decade. When Rob Lutz retired, I stayed on as a full-time technician. Anytime [Cornish] administration is like, “Oh, hey, we have kind of a weird little project” it’s been really fun to figure out how we can build those and figure out how to satiate that need. I think that’s why they came to me for the Honorary Doctorate awards, which is very sweet. I was really, really excited to learn about these artists and about their work and to try and make something that I felt like was in honor of their work and how they’ve changed the field of sculpture. That was my approach.
I’m curious if you have a favorite machine in the Fab Lab?
I do. It’s actually called a scroll saw. Love a scroll saw. Laser cutters have kind of replaced them in the detail that they can do, but man, oh man, I love a scroll saw. They even make one that’s treadle-powered so you can do all that really fine detail, like on Victorian houses. It’s known as Gingerbread– that’s how you get all the fancy, tiny, detailed stuff.
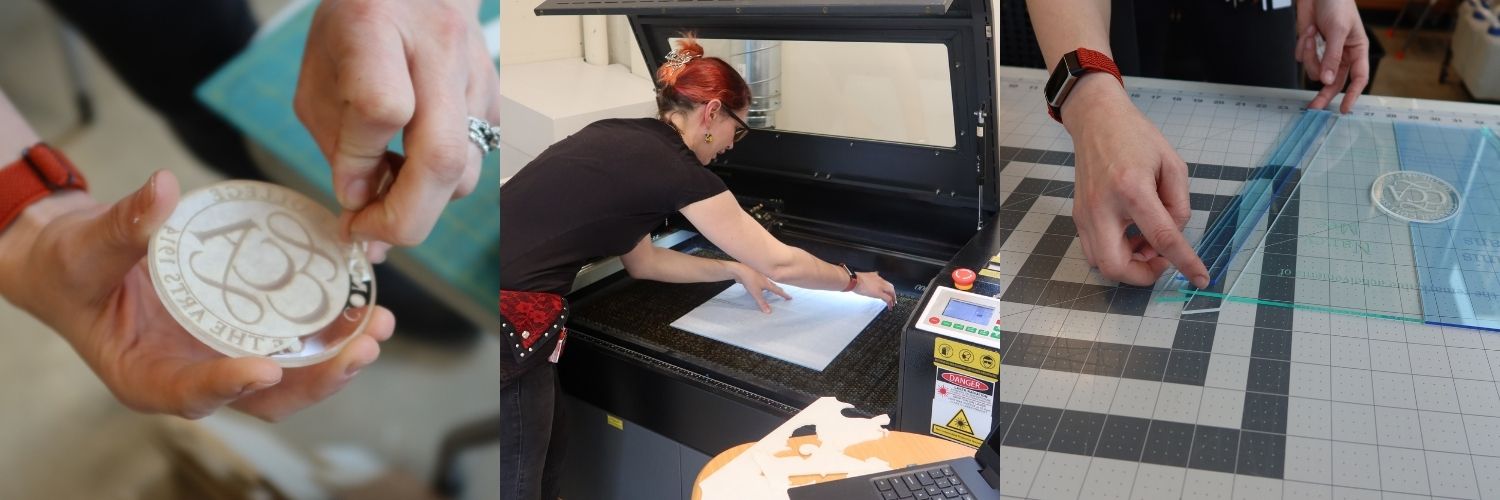
What has the process been like creating the Honorary Doctorate Awards for Dennis Evans and Nancy Mee? Any unique challenges or notable design choices along the way?
As an artist, I definitely have things that I would like to use and ways that I would like to approach [the awards]. I gave the [Cornish] board four different ideas for material choices we can make and potential directions we could go. The award that they ultimately wound up landing on is something that is simpler to fabricate than something that’s like, a crazy glass thing. It’s a little more in the realm of possibility instead of having to look outside quite so far… I wanted to incorporate Nancy’s beautiful glass without [campus] access to casting glass.
My thought process was “Okay. Here we have all this beautiful traditional sculpture, and at Cornish, we do a lot of exploring the future of sculpture. So what does that look like in this digital landscape?” In playing with material choices and design elements, we’ve really been able to marry that. We’re using a laser cutter to engrave on green edge-cast acrylic, which looks more like glass, to honor that; Then, we’re playing with a couple different colors of that glass-look acrylic to build up something like Nancy’s work. We incorporated different types of wood to get that warmth, with a lot of the geometry that Dennis touched. It’s the rule of thirds, but done in fourths. There is a lot of fun playing with music and text and geometry like Dennis’ work, right? I wanted to honor that as well.
I thought it was so beautiful that they had their books bound by the same book binder, and they even used the same strand of copper in their book. I wanted to play with that, so in the design element that the school went with there are these little copper folders on the edge to keep everything vertical– but also just as a fun element. I want to have that same strand between the two designs, as they have the thread that connects the two of them. The two of them, you can really see that they’re inspired by each other.
The award itself breaks into two pieces, but isn’t the full award until you put them together. That was kind of the way that I found to honor them both; we wanted something that would be a little bit more sentimental than a traditional award and closer to something that they would like aesthetically, right? It’s gonna have three types of wood on the bottom. Each one will be a third of the size bigger, going down to hold up the structure. It will come in half and then snap together to reveal the whole. I’m really excited about it. It took a lot of iterations to come to something that ultimately felt very simple.
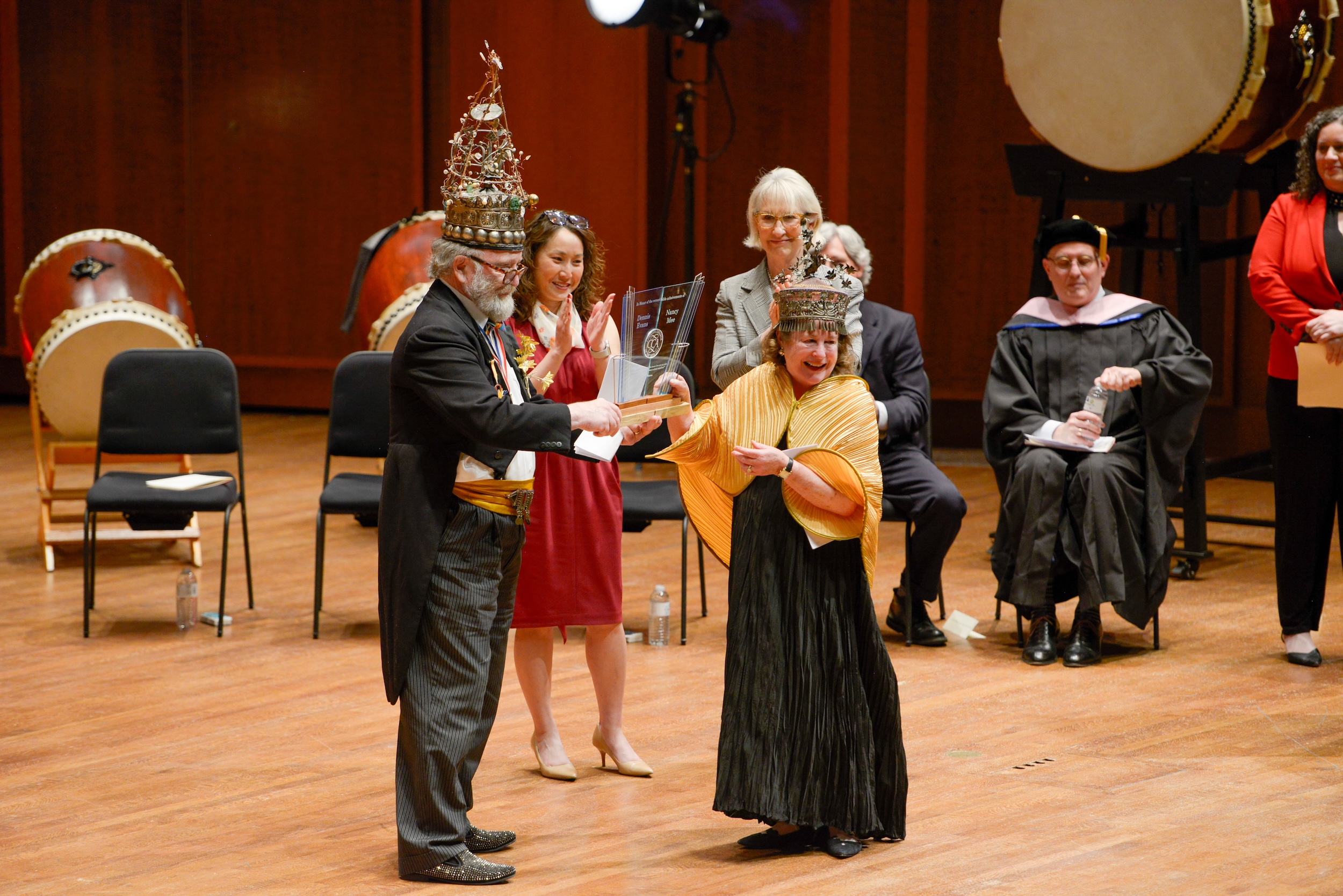
What’s your favorite part about working in fabrication and on these designs—do you prefer the design phase, problem-solving technical challenges, or seeing the final product come to life?
All of it! *laughs* right? I love being in fabrication, because I love taking an idea to completion. I also have co-workers who would remind me that I am very specific about my finishes and how stuff looks when it’s done. I do love getting to that final step of like, how do you push it just a little bit further? How do you take it to the nicest level possible? Every material is going to have something a little bit different that takes it just that little extra bit [further]. You might sand down to a 400 grit, just to make sure that it’s beautiful and polished and make that material stand out for what it is. I guess that’s my favorite.
But, I do really love the whole process. It is really easy to get bogged down with bigger projects and be like, “Oh man, I’m right in the middle of this, and I just want to be done.” It’s that pushing through and seeing it to the end that just makes it that much sweeter. There’s very little that feels as good as when you finished a huge project and you get to walk through it and you’re just like, “wow, this came together.”
Cornish is all about interdisciplinary collaboration—can you tell me a bit about any collaborative or interdisciplinary aspects of the awards you are creating?
Well, wood and copper are very traditional materials. Glass would have been more traditional, but the fact that it’s acrylic and something that we can laser cut [and engrave] to give some three dimensionality to this flat surface…that’s where it plays more into the modern technology side. We’re still hand carving the area for it to sit in, but the laser cutter really expedites a lot of the processes that you would otherwise use with glass. Fabrication is interdisciplinary in that you’re using digital and physical elements. You’re doing woodworking, you’re doing a little bit of metal working. You’re doing this acrylic work. So within the field of fabrication [the award] is interdisciplinary but there’s not a dance or jazz element to it, right?
Would you mind sharing briefly about the other awards you’re working on?
I am also working on designs for the Faculty and Staff awards. I’m doing some of that, which has been fun to bring really modern–or really traditional–woodworking and steam bending into that. For the Staff Award we’re doing some [of it] really meticulously handcrafted. For the Faculty Award, we’re doing more fun, playful sculptural elements that are going to involve the digital side of sculptural making. We’re also including some of the wood, which has been inspired by working on this award. It’ll be really fun. I’m excited.
Corey Skillman’s work on the 2025 Honorary Doctorate Awards highlights the value of thoughtful design and hands-on problem solving. From choosing materials that reflect the artists’ legacies to using both traditional and digital tools, her process is a clear reflection of the collaborative, interdisciplinary approach supported at Cornish College of the Arts. With nearly two decades of experience in fabrication and a deep connection to the college, Corey shows how meaningful work can come from a balance of skill, creativity, and intention.
Read More
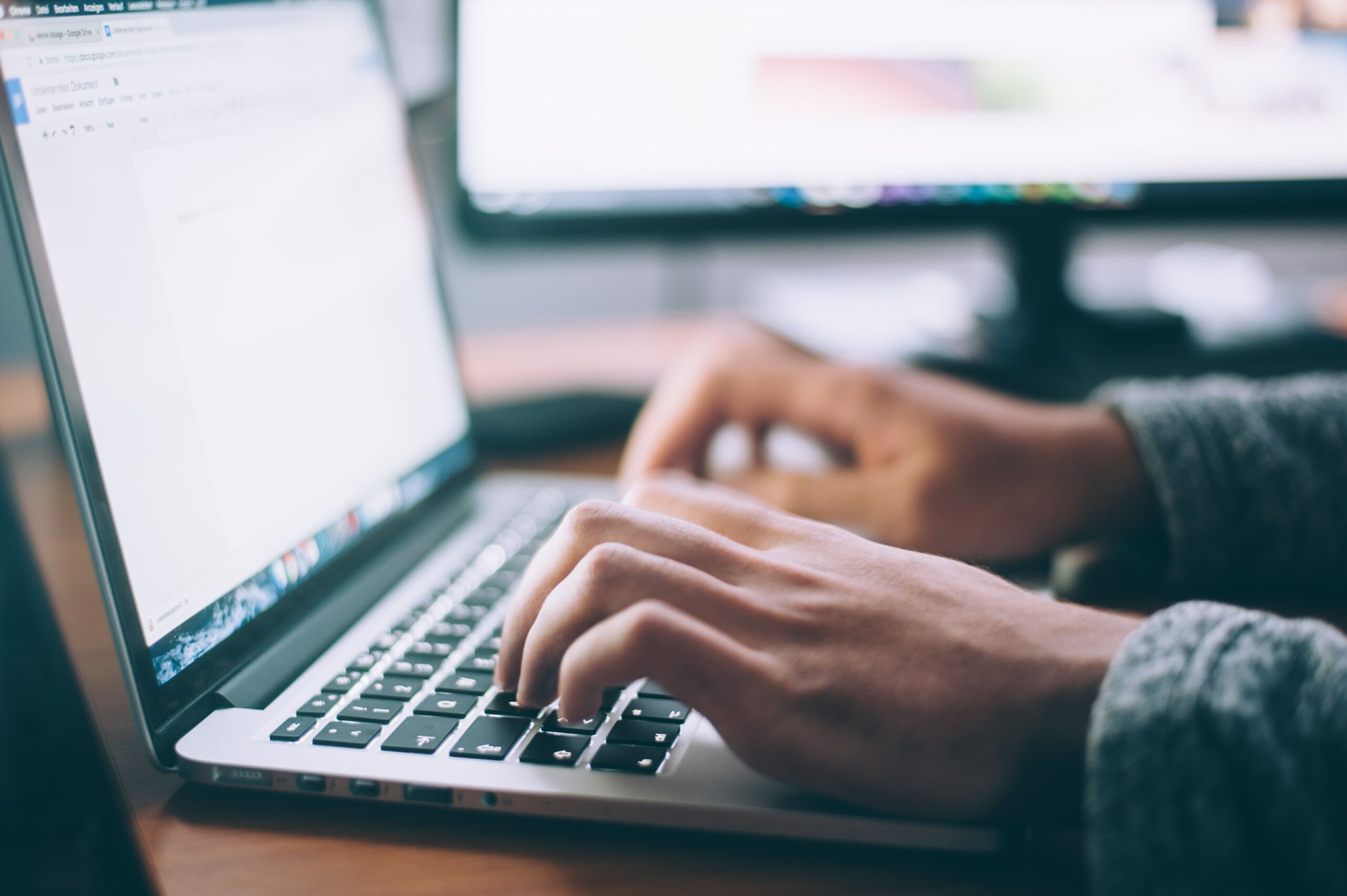

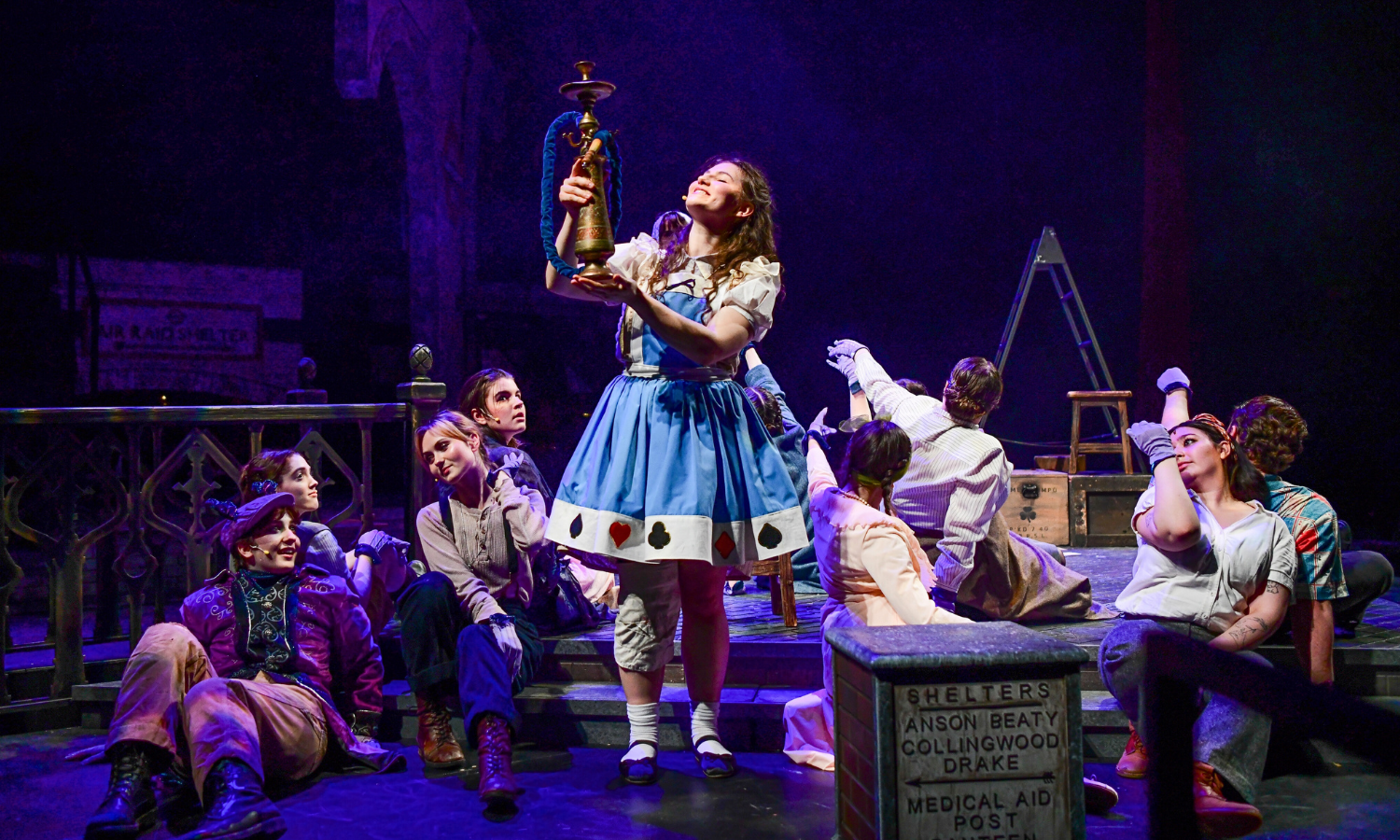
Lenora St. Blog
Grief and Whimsy: Ruby Carter and Roxy Orkney Bring Worlds to Life in Alice by Heart
Read more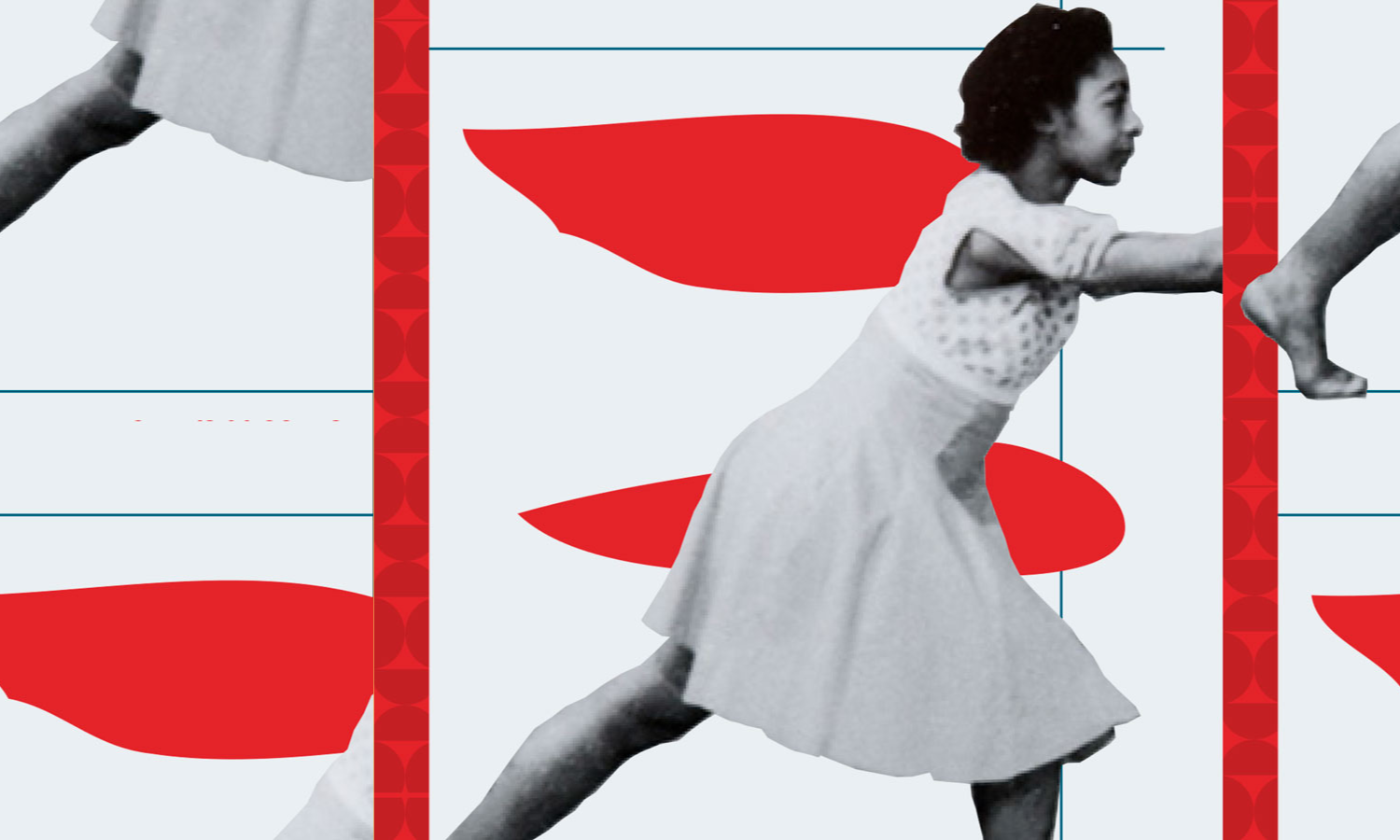